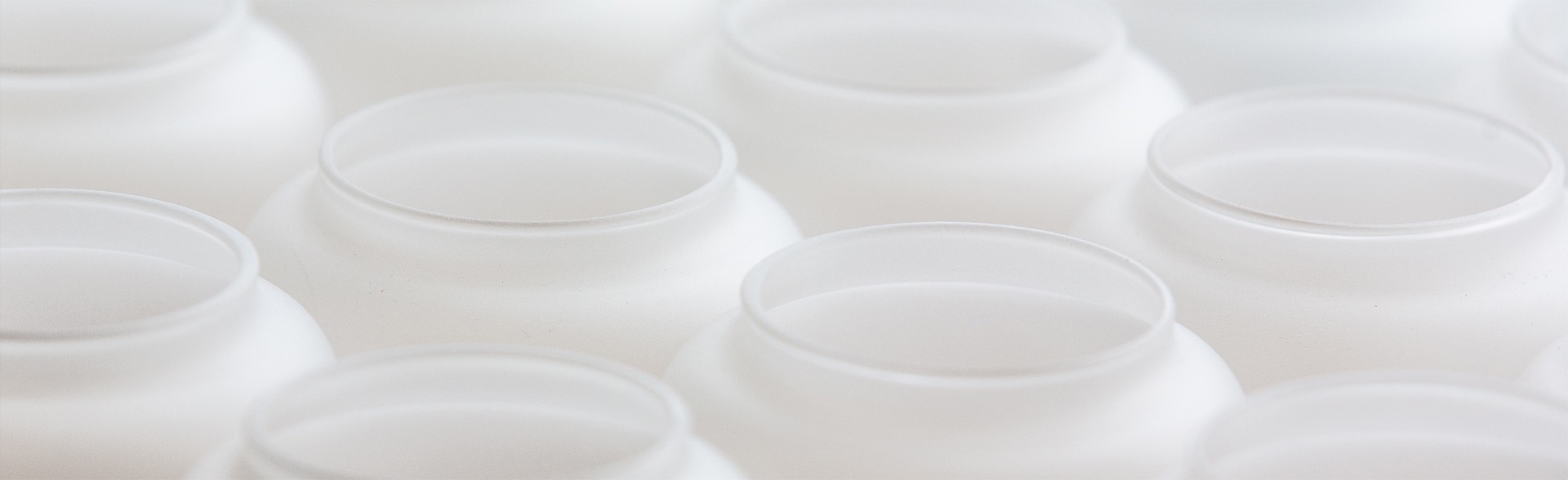
Our services
We offer our clients a wide variety of high quality custom made technical glass. Depending on your application we can help you find the most suitable solution according to your needs. Whether it is by our in house production by our skilled glass blowers and specialists, through our cooperation partners or suppliers we can find a way that fits you - from sample to large scale production.
Scientific glassblowing is a specialized craft used to create custom glassware and instruments for scientific research, laboratories, and industries. This technique involves shaping, fusing, and manipulating glass through the application of heat and controlled methods. It's an essential skill in many scientific fields, including chemistry, physics, and medicine, where specialized glass equipment is required for experiments, reactions, and precision work.
Here's an overview of scientific glassblowing, including the process and tools involved:
Key Steps in Scientific Glassblowing:
1. Selecting the Glass:
The type of glass chosen depends on the application, whether it's borosilicate glass, quartz glass, or other specialized types. Borosilicate glass is the most common for scientific work because of its thermal shock resistance and chemical stability.
2. Heating the Glass:
Glass is heated using a gas torch or furnace to a temperature where it becomes soft and malleable, generally between 1,100°C to 1,500°C (2,012°F to 2,732°F), depending on the type of glass.
Flame working is done with a torch to heat and manipulate the glass precisely. The flame is carefully controlled to prevent overheating or cracking the glass.
3. Shaping the Glass:
Once the glass reaches the right temperature, it can be blown, pulled, or molded into the desired shape. Glassblowers use various techniques to form complex shapes like flasks, tubes, beakers, or custom glass parts like adapters, funnels, and condensers.
Blowing: This technique involves creating a bubble of air inside the glass, which is then inflated into the desired shape. Glassblowers use a blowpipe or hose to inflate the glass.
Pulling: This technique is used to create thin glass rods or narrow tubes by pulling the softened glass.
Molding: Some shapes, especially repetitive ones, are made using molds that the glass is blown into.
4. Forming Joints and Seals:
Many scientific instruments require glass components to be joined together, like glass tubing or flask necks. Glassblowers form glass joints (like ground glass joints, e.g., Standard Taper Joints) by heating the ends of the glass tubes and shaping them to fit together securely.
Sealing is an essential part of the process, especially for vacuum systems, where the integrity of the seal is critical to avoid leaks.
5. Annealing:
After shaping, the glass is heated and cooled in an annealing oven, where it relieves internal stresses. This step ensures that the glass will not crack or break under normal use. Finishing:
6. Finishing:
After cooling, any rough edges or imperfections are smoothed or polished using grinders or polishing tools. If necessary, specific cuts or precision adjustments are made to ensure the glassware fits perfectly with other components or instruments.
Common Applications of Scientific Glassblowing:
- Laboratory Glassware: Flasks, beakers, test tubes, burettes, condensers, distillation apparatus, and more.
- Custom Scientific Instruments: Tailored glass equipment for specific experiments or industrial applications, such as reactors, high-vacuum systems, or chromatography columns.
- Optics: Creating precision lenses, prisms, and other optical components for use in instruments like microscopes or telescopes.
- Medical Devices: Glass components used in medical applications, such as pipettes, vials, and syringes, often for high-precision or sterile uses.
- Research: Glassblowers often create custom solutions for experimental setups, where standard lab equipment does not suffice.
Skills and Expertise:
Scientific glassblowing requires a deep understanding of the material properties of glass and a high level of manual dexterity. A skilled glassblower must be able to control the heat, shape the glass precisely, and ensure high-quality seals and joints. This craft takes years of practice to master, especially when creating complex or custom instruments.
In summary, scientific glassblowing is a blend of art and science, with glassblowers using their expertise to create highly specialized and precise equipment that is essential in research, experimentation, and industry.
Mechanical processing of technical glass like borosilicate and quartz involves shaping, cutting, drilling, grinding, and polishing the material to meet precise industrial or scientific specifications. These glasses are chosen for their thermal, chemical, and optical properties, but their hardness and brittleness make processing quite specialized.
Here's a breakdown of the main steps and methods used:
1. Cutting:
- Method: Diamond saws (often water-cooled)
- Why: Both borosilicate and quartz are hard and brittle, so regular blades can't handle them. Diamond tools reduce microcracks and chipping.
- Precision cutting: CNC machines with diamond-coated wheels or lasers (for thin sections).
2. Drilling:
- Method: Ultrasonic drilling or diamond-tipped core drills
- Cooling: Water or oil-based lubricants to prevent cracking from heat
- Special note: Quartz is harder than borosilicate, so it requires more careful speed/feed control.
3. Grinding:
- Purpose: To shape edges, bevel corners, or achieve tight tolerances.
- Tooling: Diamond grinding wheels or belts
- Process: Typically done in stages—from coarse to fine grit—to reduce stress and surface defects.
4. Polishing:
- Purpose: Improve surface finish (optical clarity or smoothness for bonding)
- Abrasives: Cerium oxide, aluminum oxide, or diamond slurry
- Technique: Lapping or pitch polishing for flat surfaces; sometimes hand polishing for lenses or curved forms.
5. Fire Polishing (Optional):
- Used for: Borosilicate, more than quartz (quartz has a much higher softening point)
- How: Flame smooths out micro-cracks and gives a glossy finish
- Note: Risk of deformation if not controlled properly
6. Cleaning:
- Process: Ultrasonic cleaning + solvents (e.g., isopropyl alcohol, acetone) or acid baths (especially for quartz)
- Why: Removes particles and residues before further assembly or coating